Looking for van conversion to refrigerated van?
- thermopartssales
- Sep 20, 2022
- 3 min read
There are plenty of manufacturers of home refrigerated van conversion kits that are happy to tell you how easy it is. However, converting a van into a refrigerated van isn’t really a simple project. Full size vans offer payload capacities up to 3500 lbs. and come in regular length and extended lengths in certain brands. If you are going to be using the refrigerated van to transport foodstuffs that are meant for human consumption you should be very cautious. If you are planning to transport sensitive foods like meat, fish, and dairy products it is just best left to this to professionals as Thermo Parts B&H.
Thermo Parts offer temperature-control solutions for full-size and compact cargo van chassis. Our customization go from thermal curtains to diamond plate floor or electric standby. We can have your refrigerated van ready for frozen, refrigerated, heated, or multi-temperature requirements.
Our standard insulation includes polyurethane foam insulation and seamless, food-safe liner, resulting in consistent temperature control and a durable cargo area. Virtually endless combinations of storage, lighting, flooring, and accessibility options ensure delivery solutions tailor-fit to your business.
There are two systems that make up the refrigeration system in a refrigerated van, and they are both equally important. They are the insulation system, and the actual refrigeration mechanism. The cooling system works by trapping the heat energy that is inside the refrigerated van’s compartment and expelling it into the outside. By the other hand, the insulation stops any more heat from leaking in. Together they ensure that the temperature inside the van drops to the required business conditions, ensuring safe transit for the products being transported.
This insulation is made of a high-density polymer foam. The foam insulation used in a refrigerated van is thicker and very durable. This insulation stops heat from entering the van. It’s a very poor conductor of heat, partly because of the many thousands of tiny bubbles of air that are embedded into the foam. This composition makes it very difficult for heat to permeate, and the thicker it is, the less heat will get in. The lowest possible temperature of the inside of the van is mostly determined by the thickness of the insulation.
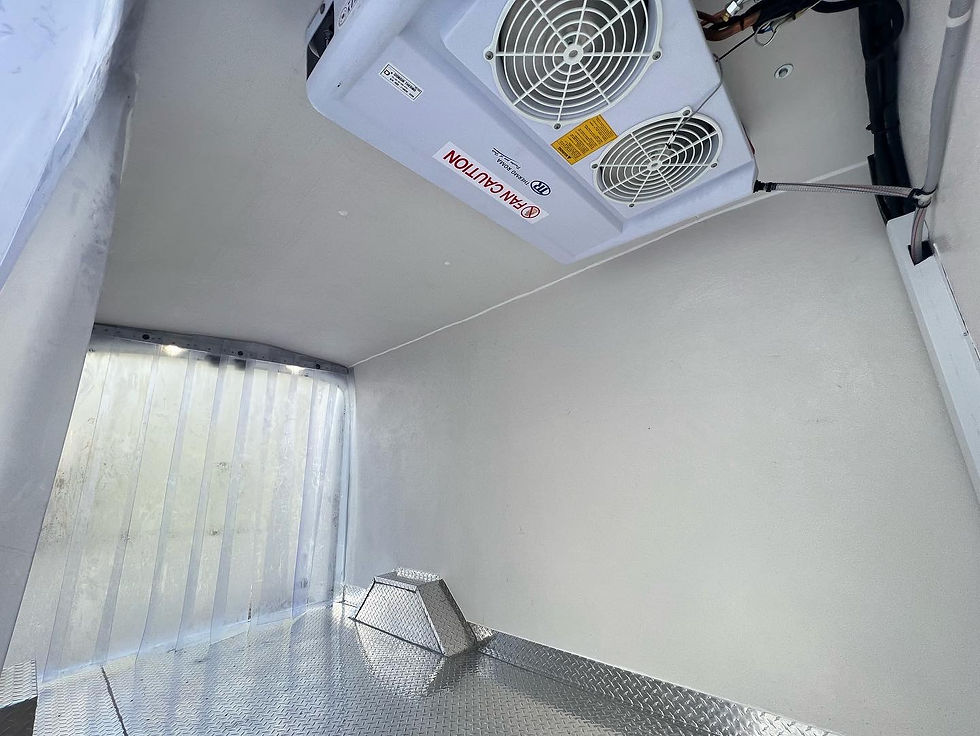
When the insulation is installed, the technicians are extremely careful to cover every inch of the van’s loading bay interior with a thick layer of foam. This avoids any gaps caused by heat from the outside or the engine to get into the chilled compartment, making the entire cooling system ineffective.
As a second stage, the foam is lined to create a hard and durable surface to stops the insulation from being damaged by the loading and unloading process. It will also protect it from spillages not going into the insulation where cleaning would be difficult.
There are two types of lining used: wet lay and dry lay. Dry lay is a layer of hard, white plastic tiles that are arranged inside the vehicle. Wet lay involves a coating that is sprayed on wet, creating a completely impermeable, smooth, and uniform surface as it dries. In our case, we create the wet lay under the dry lay and then we seal the entire area. This is because the tiny gaps in between the dry lay tiles can often become a fertile breeding ground for mold and bacteria. This can be a huge issue, particularly when you are dealing with foodstuffs being delivered for public consumption.
There are a huge number of sensitive factors to consider when converting a van into a refrigerated van. So, do not hesitate to contact Thermo Parts B&H, your +25-year specialist in this field. That way you know that you’ll get a refrigerated van that has a reliable, accurate and safe refrigeration system. We have many happy sold customers from bakery businesses, beverages, catering, floral, grocery, meal programs, mobile vending, pest control, school nutrition, pet grooming, etc.
Commentaires